箱體鑄件是機械制造業(yè)中非常重要的基礎零件之一,廣泛應用于各種機械設備中。其質量的好壞直接影響到整個機械設備的性能和壽命。那么,如何才能控制好箱體鑄件的質量呢?本文將從原材料選擇、鑄造工藝、熱處理、檢測方法等多個方面詳細解答這個問題,幫助讀者全面了解并掌握箱體鑄件質量控制的關鍵點。
一、原材料選擇
1.材質選擇
箱體鑄件常用的材質包括灰鑄鐵、球墨鑄鐵、合金鑄鐵等。不同的材質具有不同的力學性能和適用范圍。
灰鑄鐵:具有良好的減振性和耐磨性,適用于制造大型箱體和基礎件。
球墨鑄鐵:具有較高的強度和韌性,適用于制造需要較高強度和韌性的箱體。
合金鑄鐵:具有更好的耐熱性和耐磨性,適用于特殊工況下的應用。
2.原材料質量
原材料的質量直接影響到最終鑄件的質量。優(yōu)質的原材料不僅化學成分穩(wěn)定,而且雜質含量低,能夠保證鑄件的性能和穩(wěn)定性。
需要嚴格控制原材料中的有害元素(如硫、磷)含量,以減少鑄件產生缺陷的可能性。
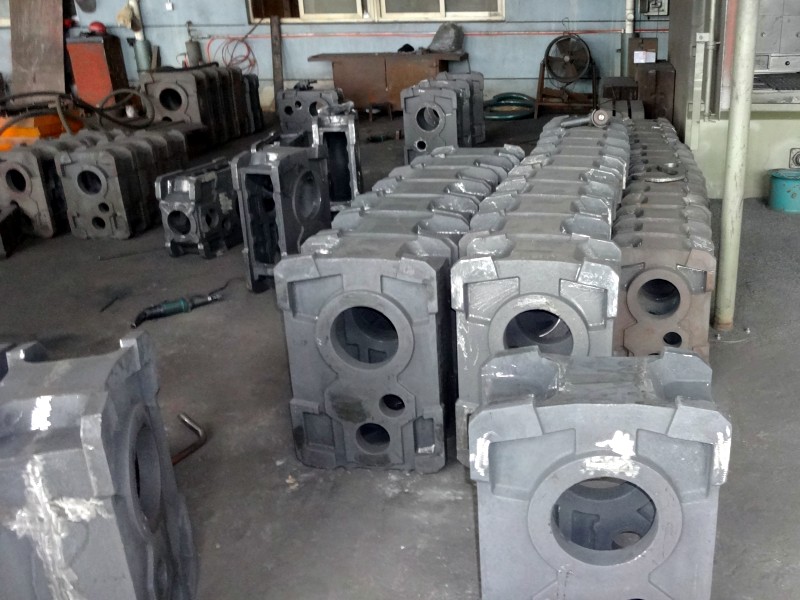
二、鑄造工藝
1.熔煉工藝
熔煉工藝是鑄造過程中的關鍵環(huán)節(jié),主要包括熔煉溫度、保溫時間和澆注速度等因素。
熔煉溫度:合適的熔煉溫度可以保證金屬液的流動性,減少氣孔和縮孔等缺陷。
保溫時間:合理的保溫時間可以保證金屬液的均勻性,避免成分偏析。
澆注速度:適當的澆注速度可以減少鑄件中的夾雜和氣孔。
2.模具設計
模具的設計直接關系到鑄件的形狀和尺寸精度。合理的設計可以有效避免鑄件變形和裂紋等問題。
模具材料:需要選用具有良好導熱性和耐磨性的材料,以保證鑄件的質量。
模具尺寸:需要根據鑄件的實際尺寸和收縮率精確計算,確保鑄件尺寸準確。
3.澆注工藝
澆注工藝主要包括澆注溫度、澆注速度和澆注方式等因素。
澆注溫度:澆注溫度過高或過低都會影響鑄件的組織和性能。
澆注速度:合理的澆注速度可以保證金屬液的平穩(wěn)流動,減少氣孔和夾雜。
澆注方式:正確的澆注方式可以減少鑄件中的氣孔和夾雜。
三、熱處理
1.退火處理
退火處理是為了消除鑄件中的內應力,改善鑄件的力學性能。通過高溫加熱和緩慢冷卻,可以使鑄件內部組織均勻化,提高鑄件的塑性和韌性。
退火溫度:根據具體材質和鑄件尺寸確定,一般在600700℃之間。
保溫時間:根據鑄件厚度確定,一般為每毫米12小時。
2.正火處理
正火處理是為了細化晶粒,提高鑄件的硬度和耐磨性。通過加熱至一定溫度后快速冷卻,可以使鑄件內部組織變得細小均勻,從而提高鑄件的整體性能。
正火溫度:根據具體材質和鑄件尺寸確定,一般在800900℃之間。
冷卻速度:根據鑄件厚度確定,一般采用水冷或油冷。
3.調質處理
調質處理是為了進一步提高鑄件的綜合性能。通過淬火加回火的方式,可以同時提高鑄件的強度和韌性。
淬火溫度:根據具體材質和鑄件尺寸確定,一般在800900℃之間。
淬火介質:根據鑄件厚度確定,一般采用水或油。
回火溫度:根據具體材質和鑄件尺寸確定,一般在500600℃之間。
四、檢測方法
1.外觀檢測
外觀檢測是最基本的質量檢測方法,主要檢查鑄件的表面缺陷,如裂紋、氣孔、夾雜等。
目測:通過肉眼觀察鑄件表面是否有明顯缺陷。
量具測量:使用游標卡尺、千分尺等工具測量鑄件的尺寸和形位公差。
2.尺寸檢測
尺寸檢測是為了保證鑄件的尺寸精度,主要使用游標卡尺、千分尺等精密量具進行測量。
游標卡尺:用于測量鑄件的基本尺寸。
千分尺:用于測量鑄件的精密尺寸。
三坐標測量儀:用于測量復雜鑄件的尺寸和形位公差。
3.無損檢測
無損檢測是目前廣泛應用的質量檢測方法,主要包括磁粉探傷、滲透探傷、超聲波探傷等。
磁粉探傷:可以檢測鑄件表面和近表面的裂紋等缺陷。
滲透探傷:可以檢測鑄件表面開口缺陷。
超聲波探傷:可以檢測鑄件內部缺陷,如氣孔、夾雜等。
4.力學性能檢測
力學性能檢測是為了驗證鑄件的力學性能是否符合標準要求,主要包括拉伸試驗、彎曲試驗、沖擊試驗等。
拉伸試驗:用于測定鑄件的抗拉強度、屈服強度等。
彎曲試驗:用于測定鑄件的彎曲強度和韌性。
沖擊試驗:用于測定鑄件的沖擊韌性。
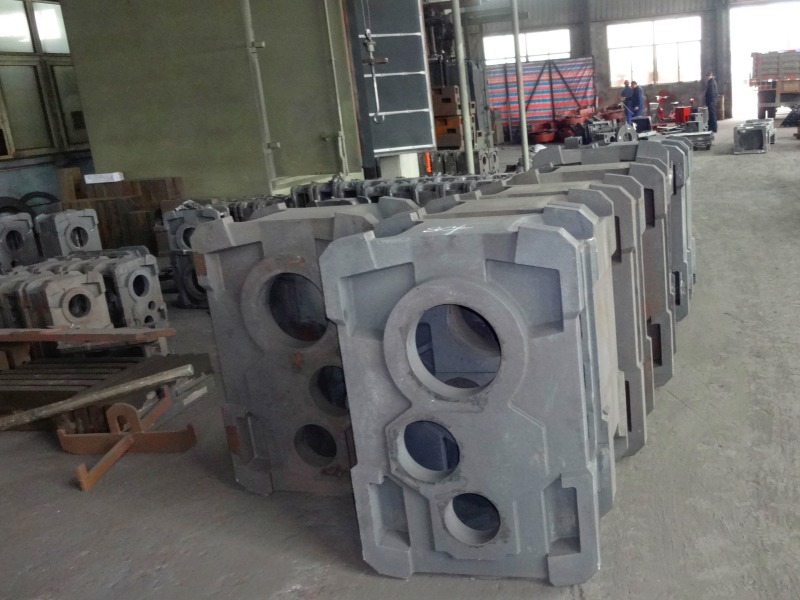
五、案例分析
為了更好地理解上述因素對箱體鑄件質量的影響,我們來看幾個實際案例:
1.案例一:某工廠生產的箱體鑄件出現大量氣孔
分析原因:該廠使用的原材料中含有較多的氣體,導致熔煉過程中產生大量氣泡;澆注工藝不合理,澆注速度過快,無法及時排出氣泡。
解決方案:嚴格控制原材料質量,減少氣體含量;調整澆注工藝,降低澆注速度,增加排氣措施。
2.案例二:某工廠生產的箱體鑄件出現裂紋
分析原因:該廠使用的模具設計不合理,鑄件在冷卻過程中產生較大的內應力;熱處理工藝不當,鑄件未充分消除內應力。
解決方案:重新設計模具,改善鑄件的冷卻條件;優(yōu)化熱處理工藝,充分消除內應力。
3.案例三:某工廠生產的箱體鑄件尺寸超差
分析原因:該廠的模具精度不夠,導致鑄件尺寸不準確;檢測方法不規(guī)范,未能及時發(fā)現尺寸偏差。
解決方案:提高模具精度,確保鑄件尺寸準確;規(guī)范檢測方法,加強尺寸檢測,及時糾正偏差。
六、總結
箱體鑄件的質量控制是一個系統(tǒng)工程,涉及原材料選擇、鑄造工藝、熱處理和檢測方法等多個方面。只有在各個環(huán)節(jié)都做到精細化管理,才能生產出高質量的箱體鑄件。具體來說:
1.原材料選擇:選擇優(yōu)質原材料,嚴格控制有害元素含量。
2.鑄造工藝:優(yōu)化熔煉工藝、模具設計和澆注工藝,減少鑄件缺陷。
3.熱處理:合理安排退火、正火和調質處理,提高鑄件的綜合性能。
4.檢測方法:嚴格進行外觀檢測、尺寸檢測、無損檢測和力學性能檢測,確保鑄件質量。
希望本文能為廣大讀者提供參考,幫助大家更好地理解和掌握箱體鑄件質量控制的關鍵點,從而提升生產水平和產品質量。如果您還有其他關于箱體鑄件的問題,歡迎隨時咨詢相關專業(yè)人士。希望本文能對您有所幫助!
如果您需要進一步了解箱體鑄件的具體應用和技術細節(jié),可以查閱相關技術資料或聯(lián)系專業(yè)的鑄造廠家獲取更多信息。希望本文能幫助您在實際生產中更好地控制箱體鑄件的質量,提高生產效率和產品競爭力。
一、原材料選擇
1.材質選擇
箱體鑄件常用的材質包括灰鑄鐵、球墨鑄鐵、合金鑄鐵等。不同的材質具有不同的力學性能和適用范圍。
灰鑄鐵:具有良好的減振性和耐磨性,適用于制造大型箱體和基礎件。
球墨鑄鐵:具有較高的強度和韌性,適用于制造需要較高強度和韌性的箱體。
合金鑄鐵:具有更好的耐熱性和耐磨性,適用于特殊工況下的應用。
2.原材料質量
原材料的質量直接影響到最終鑄件的質量。優(yōu)質的原材料不僅化學成分穩(wěn)定,而且雜質含量低,能夠保證鑄件的性能和穩(wěn)定性。
需要嚴格控制原材料中的有害元素(如硫、磷)含量,以減少鑄件產生缺陷的可能性。
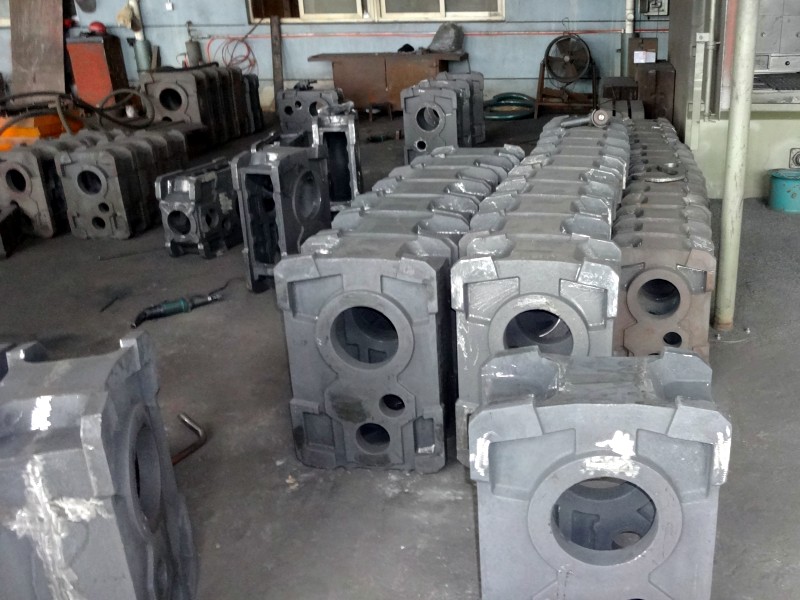
二、鑄造工藝
1.熔煉工藝
熔煉工藝是鑄造過程中的關鍵環(huán)節(jié),主要包括熔煉溫度、保溫時間和澆注速度等因素。
熔煉溫度:合適的熔煉溫度可以保證金屬液的流動性,減少氣孔和縮孔等缺陷。
保溫時間:合理的保溫時間可以保證金屬液的均勻性,避免成分偏析。
澆注速度:適當的澆注速度可以減少鑄件中的夾雜和氣孔。
2.模具設計
模具的設計直接關系到鑄件的形狀和尺寸精度。合理的設計可以有效避免鑄件變形和裂紋等問題。
模具材料:需要選用具有良好導熱性和耐磨性的材料,以保證鑄件的質量。
模具尺寸:需要根據鑄件的實際尺寸和收縮率精確計算,確保鑄件尺寸準確。
3.澆注工藝
澆注工藝主要包括澆注溫度、澆注速度和澆注方式等因素。
澆注溫度:澆注溫度過高或過低都會影響鑄件的組織和性能。
澆注速度:合理的澆注速度可以保證金屬液的平穩(wěn)流動,減少氣孔和夾雜。
澆注方式:正確的澆注方式可以減少鑄件中的氣孔和夾雜。
三、熱處理
1.退火處理
退火處理是為了消除鑄件中的內應力,改善鑄件的力學性能。通過高溫加熱和緩慢冷卻,可以使鑄件內部組織均勻化,提高鑄件的塑性和韌性。
退火溫度:根據具體材質和鑄件尺寸確定,一般在600700℃之間。
保溫時間:根據鑄件厚度確定,一般為每毫米12小時。
2.正火處理
正火處理是為了細化晶粒,提高鑄件的硬度和耐磨性。通過加熱至一定溫度后快速冷卻,可以使鑄件內部組織變得細小均勻,從而提高鑄件的整體性能。
正火溫度:根據具體材質和鑄件尺寸確定,一般在800900℃之間。
冷卻速度:根據鑄件厚度確定,一般采用水冷或油冷。
3.調質處理
調質處理是為了進一步提高鑄件的綜合性能。通過淬火加回火的方式,可以同時提高鑄件的強度和韌性。
淬火溫度:根據具體材質和鑄件尺寸確定,一般在800900℃之間。
淬火介質:根據鑄件厚度確定,一般采用水或油。
回火溫度:根據具體材質和鑄件尺寸確定,一般在500600℃之間。
四、檢測方法
1.外觀檢測
外觀檢測是最基本的質量檢測方法,主要檢查鑄件的表面缺陷,如裂紋、氣孔、夾雜等。
目測:通過肉眼觀察鑄件表面是否有明顯缺陷。
量具測量:使用游標卡尺、千分尺等工具測量鑄件的尺寸和形位公差。
2.尺寸檢測
尺寸檢測是為了保證鑄件的尺寸精度,主要使用游標卡尺、千分尺等精密量具進行測量。
游標卡尺:用于測量鑄件的基本尺寸。
千分尺:用于測量鑄件的精密尺寸。
三坐標測量儀:用于測量復雜鑄件的尺寸和形位公差。
3.無損檢測
無損檢測是目前廣泛應用的質量檢測方法,主要包括磁粉探傷、滲透探傷、超聲波探傷等。
磁粉探傷:可以檢測鑄件表面和近表面的裂紋等缺陷。
滲透探傷:可以檢測鑄件表面開口缺陷。
超聲波探傷:可以檢測鑄件內部缺陷,如氣孔、夾雜等。
4.力學性能檢測
力學性能檢測是為了驗證鑄件的力學性能是否符合標準要求,主要包括拉伸試驗、彎曲試驗、沖擊試驗等。
拉伸試驗:用于測定鑄件的抗拉強度、屈服強度等。
彎曲試驗:用于測定鑄件的彎曲強度和韌性。
沖擊試驗:用于測定鑄件的沖擊韌性。
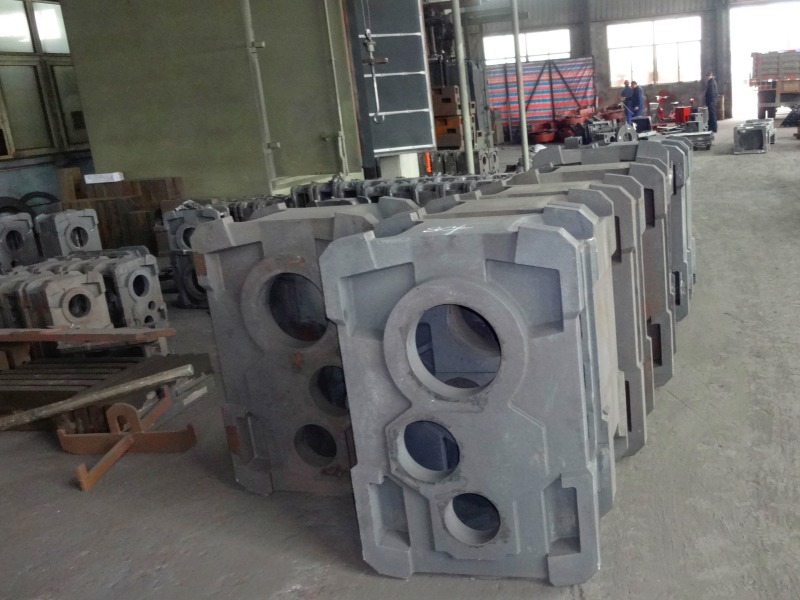
五、案例分析
為了更好地理解上述因素對箱體鑄件質量的影響,我們來看幾個實際案例:
1.案例一:某工廠生產的箱體鑄件出現大量氣孔
分析原因:該廠使用的原材料中含有較多的氣體,導致熔煉過程中產生大量氣泡;澆注工藝不合理,澆注速度過快,無法及時排出氣泡。
解決方案:嚴格控制原材料質量,減少氣體含量;調整澆注工藝,降低澆注速度,增加排氣措施。
2.案例二:某工廠生產的箱體鑄件出現裂紋
分析原因:該廠使用的模具設計不合理,鑄件在冷卻過程中產生較大的內應力;熱處理工藝不當,鑄件未充分消除內應力。
解決方案:重新設計模具,改善鑄件的冷卻條件;優(yōu)化熱處理工藝,充分消除內應力。
3.案例三:某工廠生產的箱體鑄件尺寸超差
分析原因:該廠的模具精度不夠,導致鑄件尺寸不準確;檢測方法不規(guī)范,未能及時發(fā)現尺寸偏差。
解決方案:提高模具精度,確保鑄件尺寸準確;規(guī)范檢測方法,加強尺寸檢測,及時糾正偏差。
六、總結
箱體鑄件的質量控制是一個系統(tǒng)工程,涉及原材料選擇、鑄造工藝、熱處理和檢測方法等多個方面。只有在各個環(huán)節(jié)都做到精細化管理,才能生產出高質量的箱體鑄件。具體來說:
1.原材料選擇:選擇優(yōu)質原材料,嚴格控制有害元素含量。
2.鑄造工藝:優(yōu)化熔煉工藝、模具設計和澆注工藝,減少鑄件缺陷。
3.熱處理:合理安排退火、正火和調質處理,提高鑄件的綜合性能。
4.檢測方法:嚴格進行外觀檢測、尺寸檢測、無損檢測和力學性能檢測,確保鑄件質量。
希望本文能為廣大讀者提供參考,幫助大家更好地理解和掌握箱體鑄件質量控制的關鍵點,從而提升生產水平和產品質量。如果您還有其他關于箱體鑄件的問題,歡迎隨時咨詢相關專業(yè)人士。希望本文能對您有所幫助!
如果您需要進一步了解箱體鑄件的具體應用和技術細節(jié),可以查閱相關技術資料或聯(lián)系專業(yè)的鑄造廠家獲取更多信息。希望本文能幫助您在實際生產中更好地控制箱體鑄件的質量,提高生產效率和產品競爭力。